2020 was quite the start to this decade for the construction industry. From COVID-19 to the materials shortages builders and contractor businesses faced, the 20s have brought their fair share of challenges.
Looking forward, this article covers key construction industry trends 2024 brings to the market.
More importantly, you’ll learn some strategies to keep you up to speed with these industry innovations.
Here we go!
What construction industry trends should you watch out for?
1. The rise of smart cities
The first trend to expect is the rise of smart, connected cities. This article by the Journal of Urban Technology explains smart cities as “high-tech intensive” urban solutions that connect people, data, and city elements to improve:
- Eco-friendliness.
- Economy.
- Quality of life for society.
As smart cities become more common, construction projects become more complex.
And by that, you can imagine more pedestrian sensors and WiFi-enabled lighting. Construction companies need to increase their technical know-how to stay on the same page as these developments.
How sustainability plays a role in the smart city
It’s predicted that two-thirds of the world’s population will live in cities by 2050. There’s an obvious need for smart, sustainable cities.
A few roles that sustainability plays in the construction industry trend include:
- Public transportation using real-time data and sensors to monitor high passenger volumes and accidents.
- “Smart roads” that reduce fuel costs and emissions.
- Waste management, which includes smart bins and data to improve garbage collection and waste audit. Not to mention, less fossil fuel use.
- The internet of things (IoT) to include sensors that measure air quality, noise levels, and energy.
Here’s what you’ll need to do with these insights:
- Figure out what skills and equipment smart city development requires.
- Plan for this shift, including how your government might respond.
How to overcome this key construction industry trend
Education is key to preparing for the rise of smart cities. Even taking part in skills training early will pay off for professionals who want to own this niche.
2. Increased pressure on the bottom line
Although construction revenues have been increasing in previous years, net profits in the industry are slim.
According to Deloitte, construction earnings before interest and tax (EBIT) account for 5.5% of a company’s sales. This leaves little wiggle room when it comes to unplanned expenses.
“On average, construction earnings before interest and tax (EBIT) account for only 5.5% of revenue.”
—Deloitte, 2019
To make matters worse, the cost of building materials, such as concrete and brick, is going to rise.
Among various business threats, inflation is on the rise. So, construction companies need to look long and hard at areas that can be improved to drive a better bottom line.
“Construction companies need to look long and hard for ways to drive a better bottom line.”
How to prepare for this key construction industry trend
Whether it’s negotiating prices with suppliers or automating sales workflows, construction companies need to prioritize efficiency and cost-saving.
You’ll need to consider how fluctuating materials costs will affect your:
- Budget and funds.
- Estimates and quotes.
- Sales goals.
- Bids.
3. The development of new construction materials
To increase profits and sustainability, construction companies need to:
- Reduce building material costs.
- Source sustainable building materials.
As a result, the following building materials are currently trending in construction:
- Engineered Cementitious Composite (ECC) — AKA bendable concrete. ECC contains polymer-derived fibers that make it stronger than traditional concrete. It’s cost-effective that way and has a smaller carbon footprint.
- Engineered timber — These are timber products made by engineering several types of softwood together. The result is a lumber material with the power to replace steel and concrete. This means fewer emissions and less waste during the manufacturing process.
- Recycled materials — Using recycled materials isn’t new. But recycled materials are now being used to construct entire structures (small ones for now).
- 3D printed building materials — This includes things like concrete, walls, floors, and others needed in construction. More on 3D printing and construction below.
Another strategy used to reduce material costs is modularization and prefabrication.
By adding a module assembly yard to a construction site, materials are assembled on-site. That reduces material and shipping costs.
4. A declining workforce
As far as key trends in the construction industry go, a shortage of workers is nothing new.
While the demand for construction services has been surging in recent years, the bad news is that the number of laborers hasn’t.
According to Deloitte, in 2014 construction job openings increased to 50% while new hires trailed behind at 14%. As a result, there are risks to organizations that are eager to take on new construction projects.
Without enough laborers to meet deadlines, customer satisfaction becomes challenging. So, for companies to get repeat customers it’s important that crews have enough workers.
How to handle this key construction industry trend: Investing in human resources
With construction worker count decreasing, companies need to do more with less.
Supporting your team’s efforts with more construction equipment or workflow automation are sure-fire ways to get the productivity up.
Another way you can tackle the challenge is to invest in your team. Here are a few ways construction companies can do this:
- Creating training programs, certification programs, and apprenticeships.
- Offering bonuses and performance-based incentives.
- Paying competitive wages.
Following these recommendations has the potential to:
- Reduce employee turnover, which is at the highest rate of all industries.
- Help you recruit highly-skilled laborers.
- Get an up-close look at potential hires and future leaders to develop for your needs.
- Improve client relationships as they appreciate an efficient network of workers.
5. 3D printing having a bigger impact on the construction industry
As mentioned above, 3D printing continues to play a big role in construction.
While we aren’t 3D printing homes on a mass scale yet, there are models of mansions and office buildings that were 3D printed — in record time, no less.
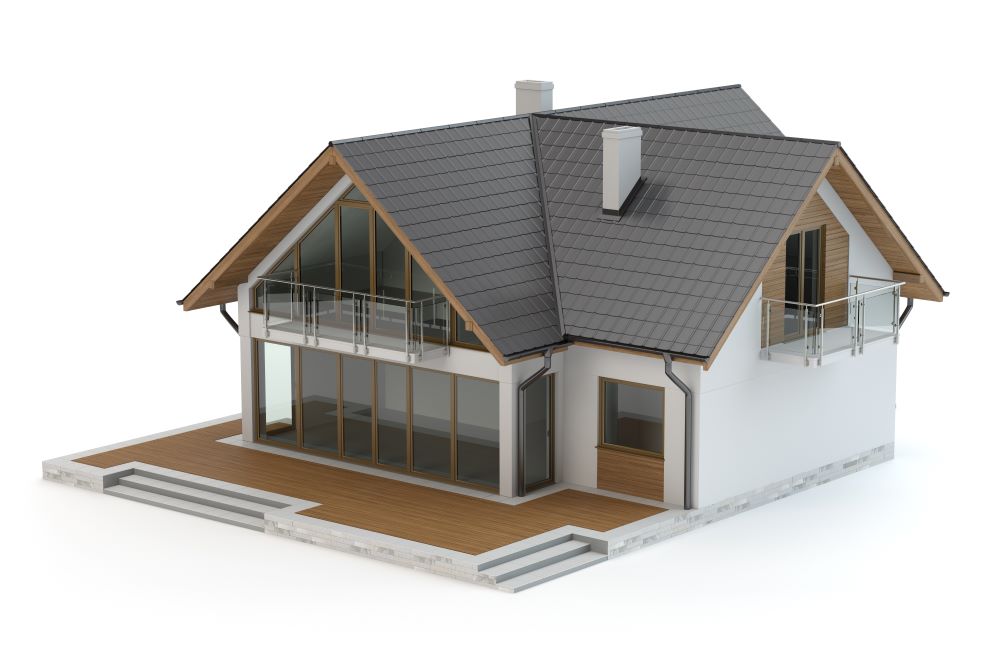
A more practical use for 3D printing in construction is for low-income and emergency housing.
The cost of an entirely 3D-printed home is currently around the $10,000 mark and there’s a possibility of that being reduced to $4,000.
And right now, 3D printing of materials, building components, and parts for construction equipment is already in full swing.
And what are the benefits? Think reduction in waste, turnaround times, and the ability to mass print custom designs without changing any machinery. It’s clear why 3D printing is a construction industry trend to have on your radar!
6. The overall trend towards tech and digitalization in construction
Necessity is the mother of invention. With labor shortages and shrinking profits, tech in the construction industry promises productivity and efficiency.
Some of the influence that tech has had on the construction industry includes:
- Robotics like mechanical arms that perform repetitive tasks such as brick-laying.
- Self-driving construction vehicles.
- Drones for inspections and land surveying increasing 239% year-over-year.
- The use of AI and simulations in collaborative building design.
- Wearable sensors for worker safety regulations.
- Smart project management like job scheduling and budgeting tools.
Tech has disrupted every industry, so it’s no surprise that various sectors in the construction industry are following suit.
Construction industry technology trends
Technological advancements are changing the construction sector. And thanks to the latest research and developers, the Internet of Things and AI are fuelling construction growth.
But what trends and events should you keep an eye out for? Here are a few expectations you should have:
- Digital collaboration software that allows teams to stay connected even when miles apart.
- New building materials to finish construction projects in a shorter amount of time.
- 3D printing with the advantage of faster access to tools and equipment.
- Robots and machines that can work on repetitive and menial tasks.
- Wearable devices like GPS trackers and biometric sensors for safer construction sites.
- New kinds of bricks made from a wide range of recycled materials, including industrial waste.
All of these developments may seem difficult to grasp and implement for your own business. But they’re worth it!
As construction business owners, you want to grow your business. So, by embracing these new trends before the competition, you’ll be sure you’re delivering the best value for your customers.
Residential construction trends in 2024
The pandemic has caused more people to realize the importance of comfort at home. As a result, market trends show that customers want more personalized touches in residential spaces.
As well as that, the looming forecast of climate change is also driving construction market trends across the world.
To make sure you’re always ahead of the curve, here are some key trends in the home-building market for 2024:
- Energy efficiency: With more people concerned about sustainability, construction industries need to prepare for building environmentally-friendly homes.
- Outdoor spaces: Being stuck at home for the past few years has inspired people to recreate natural settings at home. This means more requests for livable outdoor spaces like an exterior living room or outdoor kitchens.
- Smart home technology: Statistics show smart homes taking the world by storm. Expect more requests for programmable thermostats, clap-activated lights, and other smart appliances.
Access to more home improvement resources has also inspired homeowners. Here are some stylistic trends:
- Shiny or matte black accents on windows, doors, and furniture.
- Requests for “biophilic design” with organic materials and an emphasis on letting more sunlight and fresh air into the house.
- Maximalist designs with cultural touches, which compensated for the lack of travel during the pandemic.
Commercial construction trends In 2024
As with residential buildings, the construction market forecast shows market growth in the commercial construction landscape.
Additionally, the rise of hybrid working environments has changed the way we see offices.
Some more key trends in construction sectors are:
- Potential supply chain disruptions: Recent shortages in wood, steel, and lumber may lead to the inflation of material costs this year. Lock prices early, so they don’t surge once your project kicks off.
- Skilled labor shortages: Many construction companies are still struggling to recruit skilled construction workers, causing delays to their work process. Scout trade schools and colleges to ensure you meet labor supply requirements.
- Drone usage: Many dangerous tasks can now be done with robots and drones.
- Sustainable offices: Sustainable offices have become a priority for companies looking to build office space. Expect requests for more greenery and energy-saving measures.
- Multifunctional rooms: With more people working at home, businesses are trying to maximize space, with architecture that includes multifunction rooms and open working spaces.
Construction industry trends FAQS
How big is the construction industry?
The construction industry is one of the world’s largest industries in terms of spending.
As of November 2019, there were 10.2 million construction workers in the United States, comprising nearly 8% of the entire U.S. workforce.
Experts estimate that the construction industry is valued at 10.5 trillion USD in 2024 with an annual growth rate of 4.2%.
Many factors drive this growth, like rising infrastructure needs and increasing housing demand.
How to get out of the construction industry?
Unless you’re retiring, getting out of the construction industry likely means you need to move into a new line of work. Depending on your age and experience, this can be tricky.
To prepare yourself for a career change, you can:
- List your interests to start mapping out a new career path.
- Identify transferable skills that you picked up in construction that can be applied in other careers.
- Consider applying for an apprenticeship or have an experienced mentor take you under their wing.
Consider working as a:
- General contractor: Contractor work is a construction-adjacent job where many of your skills are transferable.
- Project manager: The organizational and time management skills you learned in construction will serve you well in this role, where you’re expected to keep track of deadlines and project budgets.
Is there a concrete shortage in 2024?
Parts of America are going through a concrete shortage in 2024. There’s a high demand for concrete in the construction sector, as well as low supplies. This results in high concrete prices.
This concrete shortage may be attributed to factors such as:
- Supply chain interruptions.
- Carrier fleet service hour changes and loading restrictions.
- Limited capacity on cargo trains.
If your construction company is affected by the concrete shortage, lock suppliers in earlier or change your construction methods.
Luckily, this shortage is expected to be temporary, and supply should resume to normal in the second half of 2024.
Download your free construction estimate template
Struggling to calculate job costing and provide accurate estimates to your customers?
Let this free construction estimate template do the work for you.
If you don’t see the download form, download template here.
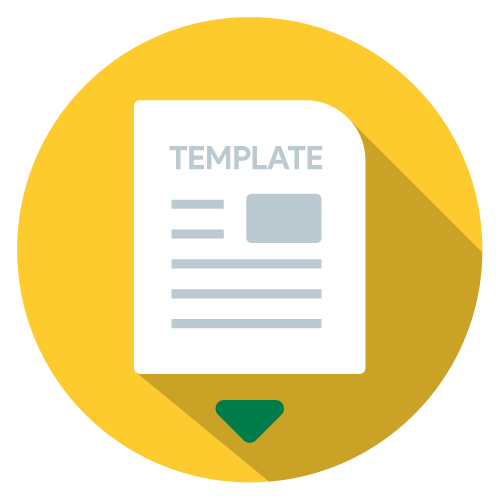
Looking forward: Key construction industry trends to come
The key trends in the construction industry highlight the important role technology plays in the future of construction. Looking into this next decade, you can expect:
- Urban development to become more complex.
- Construction costs to increase.
- More employee incentives to support a declining workforce.
When you embrace the changing landscape of the industry, you can expect more opportunities.
Watch our demo to see how Method CRM grows your business.
Image credit: Yancy Min via Unsplash