How to price a drywall job
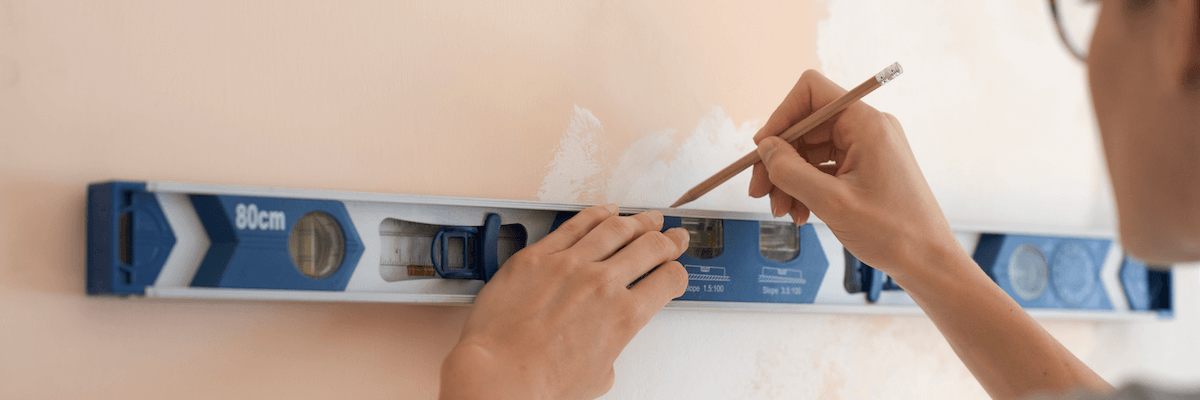
Learn what to consider when estimating drywall costs.
Drywall, also known as sheetrock panel, may not be the most exciting material, but it is an essential component of many homes.
For contractors, drywall repair or installation is one of the simplest tasks of any construction job. However, before the installation process, you must complete the sales process by estimating drywall materials and labor costs.
Estimating the costs of drywall installation or repair is a complex task, as every job is different. You can calculate most costs based on room measurements, so offer each prospective customer a custom estimate.
In this guide, you’ll learn how to price a drywall job. In particular, you’ll:
- Learn what to consider when estimating drywall costs.
- Discover the easiest way to finish drywall jobs.
- Learn how to create a drywall estimate example template.
Drywall estimating rule of thumb
The drywall estimating rule of thumb suggests that you estimate one drywall sheet (4 ft x 8 ft) for every 32-48 square feet of wall surface. When estimating paint, estimate around one gallon for every 350-400 square feet of wall area.
As a drywall contractor, it is difficult to determine the average cost of a job and answer: how much drywall do I need?
It may sound like a safer decision for your business to overestimate, but fair trades pricing is a top priority when it comes to creating an estimate.
Your customers are looking for a reliable drywall contractor, and presenting them with an accurate estimate is their first sign of your credibility.
For any construction job, you want your estimate to be as accurate as possible. Having the actual cost of a job differ from the estimated cost can negatively impact your business.
Overestimated costs mean that your customer ends up paying more than necessary. If they notice that your estimate is inflated, they may choose not to go with your services or you may be eliminated from the bidding process.
On the other hand, underestimated costs leave no room for potential unforeseen costs. Based on our firsthand experience, either your customer ends up blindsided by being told they need to pay more, or you cover the costs and lose revenue.
An accurate cost estimate demonstrates that you are knowledgeable and enhances your customers’ trust. If you have trouble completing an accurate estimate, consult a general contracting pricing guide for help.
Let’s talk about how to accurately estimate the cost of drywall jobs.
How to estimate drywall jobs
The final cost estimate of a drywall job depends on a few factors, including:
- Whether it is drywall installation or drywall repair.
- How many sheets of drywall you need.
- Cost of material and labor.
- Job size and location.
If you don’t see the download form, download your template here.
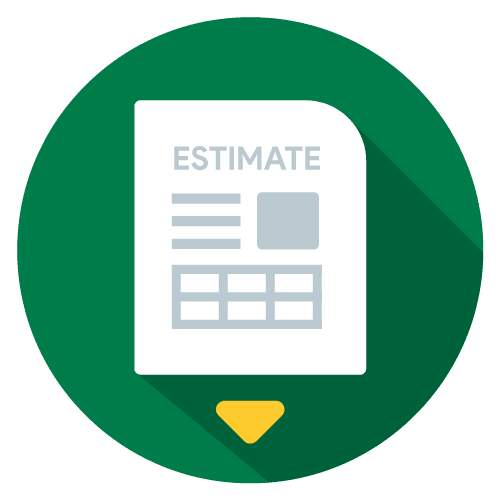
Our findings show that these cost factors have many different components to consider within them. If you’re a general contractor, make sure that your template is specifically designed for drywall. It may be tempting to modify the same template for different jobs, but don’t, as a drywall estimating template looks completely different from an HVAC estimating template.
One of the largest determining factors in a drywall estimate is the size of the job. It may take longer to estimate a large drywall job, but it doesn’t have to be more challenging than estimating a smaller job.
Estimating large drywall jobs
A large drywall job is one that requires more than 75 sheets. As a drywall contractor, it is best to use square footage as the baseline for estimating the cost of installation.
Remember, square footage refers to the surface that the drywall covers, not the square footage of the house.
Estimating small drywall jobs
Our research indicates that for most contractors, a drywall job is considered small if it is for no more than one residential room. This may also include drywall repair, which can range from fixing a crack to replacing entire panels.
Even if it is a basic project, it is still important to break down your estimate into labor costs and material costs to cover all your bases.
Depending on how small the drywall job is, it may be more efficient to create your estimate based on how many hours the job will take rather than the square footage.
Cost of material
Detailing material costs will likely be the bulk of your drywall estimating template.
You want to create a detailed drywall estimate listing the materials required for the job. Do your research and stay up to date with the current costs of materials to create your estimate quicker and more accurately.
Let’s take a closer look at the materials you need for drywall installation, and how to calculate them and other costs.
How many sheets of drywall do I need?
When planning your drywall project, accurately quantifying the number of sheets you need is crucial.
To calculate this, you must measure the square footage of the area to be drywalled, as your price is impacted by the height of the ceilings and number of openings (e.g. doors, windows).
Drywall comes in 4×8 foot panels, so you need to:
- Tally the total square footage.
- Divide by 32 (the square footage of one panel).
Remember to factor in the type of drywall material and thickness, as these impact the number of sheets you need. Always confirm your calculations to ensure you have enough supplies and drywall.
How to determine competitive rates/pricing for drywall jobs
Do competitive research
To establish competitive pricing, you should survey local market rates and evaluate the experience and expertise of the contractor workforce in your area.
It’s essential to:
- Weigh the customer reviews and testimonials.
- Gauge the perceived value of the services offered.
- Analyze market trends and industry standards.
- Validate your pricing against economic factors such as inflation and material costs.
Depending on the references and reputation of the contractor taking on the project, you can upcharge or discount your pricing, as it generally reflects the experience of the contractor.
This research will help you finalize rates that are competitive with other contractors in the area while ensuring you meet profitability goals.
How to calculate drywall profit margin
Calculating your profit margin involves taking into account:
- Labor and materials.
- Overhead and business expenses.
- Additional fees such as cleanup and disposal costs.
Your profit margin should reflect the experience of your contractors and include a markup for profit.
It must also consider any repair or preparatory work needed that factors in the complexity of the project. A transparent cost breakdown that is detailed in a written estimate or quote helps with customer communication and consultation.
How to calculate drywall markup
To calculate drywall markup, assess the total cost of:
- Supplies.
- Labor.
- Operating expenses.
- Overhead.
Make sure your markup includes potential additional expenses and incorporates potential discounts or promotions.
Note that markup varies based on the type of drywall used and adjusts for regional differences.
Remember, your price is subject to negotiation with the client, so be ready to justify how your pricing is competitive and highlight the quality of the materials.
Pricing drywall jobs — What to include in a drywall estimate
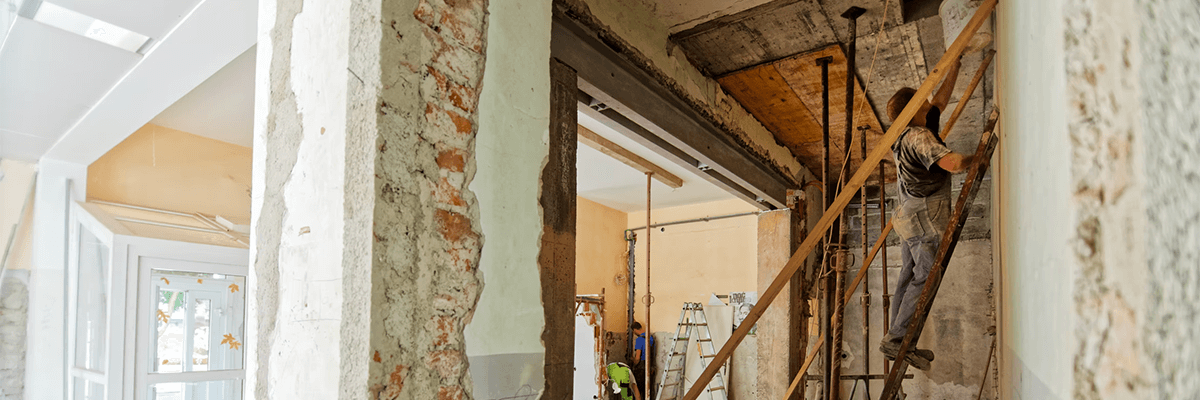
Image credit: Milivoj Kuhar via Unsplash
When pricing drywall jobs, your estimate should be comprehensive with itemized costs. It should include:
- Material and tool costs.
- Labor costs associated with the drywall work.
- Drywall installation method (e.g., hanging, taping, mudding).
- Drywall finish level.
- Additional services such as insulation or painting.
Additionally, here are some often-forgotten factors you’ll need to account for in your final estimate:
- Geographic location, considering state and local regulations and licensing.
- Insurance and liability coverage.
- Material supplier relationships.
- Specialized drywall requirements (e.g., fire-resistant, soundproofing)
- Sustainability of materials.
Your estimate should allow for adjustments for change orders or scope changes. Make sure to include:
- Payment terms and schedule, including payment methods accepted.
- Any warranty or service guarantee.
- Payment plans or financing options (if offered).
- Discounts or special offers (if applicable).
An ideal place to include these details is in the footer of your estimates.
Finally, most of your drywall estimates will detail the materials you need to complete the job. The materials that you may need for drywall installation include:
- Sheetrock panels (drywall sheets).
- Joint compound (drywall mud).
- Drywall screws.
- Drywall tape.
- Corner beads.
- Tools that you do not already have.
Determining how much of each material requires you to see the workspace and take measurements.
As per our expertise, we’ve detailed all the measurements you need to take and explained how to calculate the amount of material you need. Here are some measurements you’ll encounter when learning how to price a drywall job.
Measure square footage
Our findings show that how much material you need for drywall installation depends on the total square footage of the areas where the drywall will be installed. This may include walls and ceilings.
When you measure square footage, check the area for any obstacles, such as electrical work or plumbing, that may get in your way.
To measure the square footage:
- Multiply the width times the height of each wall area.
- Add them all together.
This gives you the total square footage and a jumping-off point for the total cost of materials.
If the job is drywall repair, then you have to measure the area where you will be either filling in with a joint compound or installing a new drywall sheet.
Many ask, “How many square feet does a sheet of drywall cover?”, and this depends on the size of drywall sheet. A 4 x 8 sheet covers 34 square feet and a 4 x 12 sheet covers 48 square feet.
Estimate drywall sheets
Our research indicates that the point of confusion is often, “How to calculate how many sheets of drywall I need?” Here’s how to calculate number of drywall sheets needed:
- If you use 4 x 8 sheets, you will divide the total square footage of the area by 32.
- If you use 4 x 12 sheets, you will divide the total square footage of the area by 48.
For example, if your total square footage is 2,000 square feet and you’re using 4 x 12 sheets, your calculation will be:
2,000 square feet divided by 48 = 50 sheets
The above number is how many sheets you need to complete the job. In terms of pricing, it is best to factor in the cost of drywall sheets plus an additional 10% for waste and odd cuts. In the above example, this equals 5 extra sheets, for a total of 55 sheets.
The same rules apply to ceiling drywall sheets.
Estimate drywall tape
Those new to the industry often struggle with “How much drywall tape do I need?”. Based on our observations, the answer is probably more than you think!
Our team discovered through using this product that most rolls of drywall tape or joint tape contain 500 feet, but you will most likely need more than that for a substantial drywall project.
Measure the perimeter of each drywall sheet, then multiply it by the number of sheets needed. Examples below:
- The perimeter of a 4 x 8 sheet is 16 feet.
- The perimeter of a 4 x 12 sheet is 20 feet.
If you use 50 4 x 12 sheets, your calculation will look like this:
50 x 20 = 1,000 feet
For this project, you need at least 1000 feet of tape. If your rolls are 500 feet long each, you’ve determined that you need to add the cost of two rolls to your estimate.
Based on our firsthand experience, it is best to add the cost of an extra roll for a total of 3 rolls of drywall tape.
Pro-tip: Use formulas like the above when figuring out how much to charge for drywall mud and tape.
Cost per square foot for mud and tape drywall jobs
On average, the labor and material cost to mud and tape drywall is between $1.50 and $3.50 per square foot.
Our findings show that there are three factors that influence drywall finishing costs:
- Room size: Larger rooms have more drywall to finish.
- Finishing type: More elaborate finishes are used when preparing the wall for paint or wallpaper and cost more.
- Local material costs: Material prices in your area may vary, so adjust your finishing rates according to local averages.
Estimate drywall mud
Once you know how many drywall sheets you need, estimate how much joint compound, or drywall mud, to use.
Our investigation demonstrated that every contractor has a preference when it comes to estimating drywall mud. The amount of drywall mud you need varies based on a few factors:
- The types of tape that you use.
- Whether you do drywall installation or repair.
- The amount that you typically apply.
To estimate the total amount of mud you need for a job, multiply the amount you need per square foot by the total number of square feet you will apply it.
If you don’t already have the amount of drywall mud you apply, estimate 0.053 pounds of mud per square foot of drywall. Here is what the calculation would look like for 2,000 square feet of drywall:
2,000 x 0.053 = 106 pounds of joint compound
Drywall mud per sheet
Every square foot of drywall usually needs 0.05 pounds of sheetrock joint compound or “mud.” This comes out to 1.5 to 2 pounds of mud for every 4×8′ drywall sheet.
Based on our firsthand experience, if your drywall has texture, you need to provide extra mud. Generally, every 50 to 150 square feet of texture needs one extra gallon of mud. Keep in mind that heavier textures tend to need more mud than lighter textures.
An easy way to account for how much drywall mud you need for a project is to count how many sheets of drywall you plan on installing. For instance, a room with 12 drywall sheets would require 24 pounds of mud.
Estimate drywall screws
The cost and number of drywall screws will be determined by a few factors:
- The framework spacing.
- Whether there are metal or wood studs under the drywall.
- The length of the screws needed for the thickness of the drywall.
Through our practical knowledge, the easiest way to calculate how many drywall screws you need is to estimate one screw per square foot of drywall installed.
A common question is “How many drywall screws per sheet?” The answer — expect to use:
- 32 screws per 4 x 8 drywall sheet.
- 48 screws per 4 x 12 drywall sheet.
As per our expertise, in the case of drywall screws, the more the better. As with all other materials, add 10% for waste.
Estimate corner beads
To finish a drywall installation, you need to apply corner beads to the corners of the walls to make them crisp and professional looking. You can estimate the corner beads by counting the number of outside corners for the entire job. Plan to use one full corner bead per corner, using either an 8-foot or 10-foot bead.
Hours to finish drywall job
Based on our observations, drywall jobs take three days to finish, with around six to seven hours of labor.
Most drywall finishing jobs are multi-day processes. Taping and mudding drywall joints take a short time to complete, but you need to let the mud dry for 12 to 24 hours before applying the next coat.
Labor costs to finish drywall jobs
Our findings show that while the cost of material is somewhat standard, the drywall labor cost is what differentiates your business from the competition.
The drywall cost per hour for labor can add up quickly, so it’s important to estimate as accurately as possible to avoid any surprises to your customer.
Here are some factors to consider when estimating labor costs:
- Time: The amount of time that it takes to complete a drywall job determines total labor costs. If you work on another project at the same time for the customer, such as roofing, separate how much time each job will take in your estimate.
- Type of job: You may charge more in labor for complex drywall jobs that require advanced skill rather than completing a simple drywall repair.
- Number of workers required: A drywall job is typically performed by a crew of 2, but a larger job may require more workers.
- Pay: The amount you pay your workers isn’t the only factor to consider, but how you pay them as well. Their pay may differ depending on if you have employees or use subcontractors. You may choose to pay your workers a lump sum for a smaller job or a drywall contractor hourly rate for a bigger job.
To estimate labor costs, you can:
- Charge based on the square footage of the area where you will install the drywall.
- Use your workers’ hourly labor rates to establish a base rate.
The second approach is usually more accurate. For example, let’s say that you estimate a large drywall job is going to require 6 hours of labor, and it will take 2 workers to complete the job. If you pay each worker $20 per hour, your base labor rate is $40 per hour.
Your calculations will look like this:
$40 base rate x 6 hours = $240 in total labor costs
If you have employees, you will also have to consider the cost of labor burden, which is the cost of each employee outside of their hourly wage. These costs can include:
- Payroll taxes.
- Insurance.
- Benefits.
Calculating labor burden depends on where you live, what your company offers as a benefits package, and how much each worker makes.
Calculating labor costs may sound complicated, but using software to create a drywall estimating template will make this process much easier.
Other costs to consider
Basic materials are not the only costs to consider. There are many other costs that you may accrue depending on different factors, such as equipment delivery and the current building codes.
Miscellaneous costs that you may also have to apply include:
- Transportation costs to travel to and from the job site.
- Cost of project supervision.
- Cost of debris removal and cleaning.
- Sandpaper.
- Permit fees and insurance.
- Paint costs if you are also painting the drywall area.
Markup and overhead
Once you figure out your costs, add markup for profit and overhead costs.
Overhead includes the soft costs of your business that are not associated with any specific job. This may include:
- Trucks.
- Tools and equipment.
- Marketing and accounting.
Profit is what is left over for your business after you pay all of the costs and overhead.
The markup for profit you set depends on a few factors:
- Location.
- Job size.
- Size of your company.
In general, smaller businesses set a markup of 15-25%, but it is up to you to determine the markup percentage for fair profits for your business.
When pricing drywall jobs, ensure that your estimate:
- Is updated regularly to match industry standards.
- Considers the quality of materials used.
- Weighs the current market rates.
By doing so, you provide a clear, detailed, and competitive estimate that adjusts based on customer feedback and preferences.
Flat-rate vs. hourly rates for drywall jobs
There are multiple ways to learn how to price a drywall job. Choosing the right pricing structure for drywall work is critical to meet customer expectations while ensuring profitability.
No matter your pricing model, the total cost of your estimate:
- Is influenced by the size and scope of the job.
- Is influenced by the project’s timeline.
Whether you opt for hourly pricing or flat-rate pricing your decision should reflect:
- Contractor experience.
- Market demand and competition.
- Complexity of the job.
Hourly pricing (time + materials)
Hourly pricing is often preferred when the scope of a drywall job is not well-defined, as it gives you more flexibility. For example, hourly pricing factors in any potential risks or challenges that could extend the project timeline, as it doesn’t impose a time limit.
This method takes into account labor and materials and presents figures transparently. Clients can see the breakdown of material and tool costs (e.g., screws, joint compound, tape) and labor hours.
It’s important to consider additional fees (e.g., overtime, emergency services) and to be clear about these in your written contract or agreement when learning how to price a drywall job.
Hourly rates are influenced by the:
- Size and scope of the job.
- Number of rooms or spaces.
Flat-rate pricing
Flat-rate pricing is based on square footage. It is used when the contractor has a clear understanding of the project’s requirements.
This model includes a markup for profit and includes overhead costs by taking into account:
- Drywall accessibility.
- The drywall finish level (e.g., smooth finish, textured finish).
- Any additional services (e.g., insulation, painting).
For flat-rate pricing, you need to consider every element of the job. For example, you must factor in:
- Economic factors (e.g., inflation, material costs).
- Environmental considerations (e.g., sustainable materials).
- Warranty or guarantee included in your contract.
Hybrid pricing
Hybrid pricing combines elements of both hourly and flat-rate pricing. It gives you the flexibility of hourly billing to cover unforeseen complexities, and the predictability of a flat rate for well-defined portions of the job.
This approach is particularly effective when the job includes both standard drywall work and special requirements, such as the removal of existing drywall (if applicable). It accounts for special features or designs better than the more rigid models.
In all pricing models, it’s essential to create a plan that:
- Includes permits and inspection fees (if applicable).
- Considers any repair or preparatory work needed.
- Ensures that your pricing structure is transparent with itemized costs.
This helps in establishing trust and ensuring that all legal considerations (e.g., contract disputes) are adequately addressed.
How to find a drywall contractor
Here’s how you can find a good drywall contractor whether you’re a homeowner, property manager, or general contractor:
- Ask friends and family to see if they have recommendations.
- Search online for drywall contractors for hire.
- Put out a call for drywall contractors in online and offline media.
When you have a pool of candidates to choose from, you need to make sure that they’re the right person for the job. Consider these factors when selecting your contractor:
- Level of experience: Look for a contractor with at least five years of experience. This ensures they have all the necessary skills to finish your project.
- Quoted price: Don’t choose a contractor simply because they bid the lowest. Compare quotes from several contractors and choose the one that gives you a reasonable price for the work that needs to be done.
- Personal factors: Ask to meet the contractor and have a chat before deciding on hiring them. This helps you identify and smooth out any personality conflicts before the work starts.
- References: Ask for references from previous clients. Be thorough and ask about the contractor’s quality of work, timeliness, and post-work cleanup.
Writing an estimate for drywall services
To recap, whether you are going to install or repair drywall, your estimate should include:
- Material costs.
- Labor costs.
- Miscellaneous costs.
- Overhead and profit markup.
A drywall estimating template keeps you consistent and makes sure that you don’t forget to factor in any costs.
Prospective customers may not accept your estimate without trying to negotiate with you, but having a detailed drywall estimate puts you in a good position to demonstrate why your business is the best choice.
If you’re participating in a bidding process, writing a compelling drywall service proposal may be your only chance to convince a potential customer to choose your business.
When writing your proposal, be sure to follow the guidelines set out by the buyer, and ask any clarification questions if necessary. An estimate that takes into consideration any warranties or guarantees offered also increases business opportunities.
Whether your potential customers come to you, or you’re submitting a proposal as part of a bidding process, presenting an accurate estimate is the defining factor in turning a prospect into a customer.
No matter the circumstances under which you need to present an estimate, using software to create a drywall estimating template makes this process quick and efficient.
Even if you’re a general handyperson, empowering your estimates with technology is the best approach.
Templates are helpful, but what if we told you that you could generate a perfect invoice in seconds? Our free tool does the hard work, so you get paid faster.
Drywall estimate FAQs
- How do I calculate how much drywall I need?
- Should I use a drywall estimate Excel sheet?
- How do you bid on a drywall job?
- How much drywall do you need for a 2000 sq ft house?
- How do you calculate sheetrock for a room?
How do I calculate how much drywall I need?
To calculate how much drywall you need for a drywall installation, you need to:
- Measure the square footage of the surface.
- Determine what size drywall sheets you will be using (4 x 8 or 4 x 12).
- Divide the square footage by the perimeter of the size sheet you choose.
Pro-tip: Divide by 32 for 4 x 8 sheets and divide by 48 for 4 x 12 sheets. The result is how many drywall sheets you need.
Here is an example using 4 x 12 sheets for 2,000 square feet:
2,000 square feet divided by 48 = 50 sheets
Should I use a drywall estimate Excel sheet?
Using Excel is a great way to create an estimate. However, when using Excel, it is worth creating a drywall estimating template for consistency and to reduce error.
For the most accuracy, it is best to use a drywall estimate template or estimating software like Method:Field Services.
Drywall estimating software lets you:
- Share accurate drywall quotes.
- Create estimates on the go.
- Save time on double data entry.
- Quickly convert estimates to invoices.
Using software automates the process of estimating so that you can deliver your estimates quicker and start working with your customers sooner.
If you don’t see the download form, download template here.
How do you bid on a drywall job?
To bid on a drywall job, you need to submit an offer to the employer or client.
Bidding on a drywall job is one of the best ways to land a contract as a drywall contractor, but you may need to contend with other contractors to get the job.
To boost your odds of landing a drywall contract, you need these three things.
- A short description of how you can fulfill the client’s needs.
- Details on your past drywall jobs, including testimonials and references to demonstrate your experience and quality.
- An accurate estimate of how much it takes to finish the requested job.
Out of all the above, your pricing estimate will likely be the crux of your client’s decision. That’s why you need to make your estimate is reasonable and can still net you a profit.
Here’s each step to accurately calculate hourly rates for your drywall jobs:
- Calculate your monthly operational and business expenses.
- Determine your expected monthly revenue and profit margin.
- Define how many hours you expect to work monthly.
- Add your expenses and margin.
- Divide this number by your work hours to arrive at an hourly rate.
How much drywall do you need for a 2000 sq ft house?
You need roughly 150 to 160 4×8′ sheets of drywall for a 2000-square-foot home. In total, that’s about 8,000 to 9,000 square feet of drywall.
However, this number can increase or decrease depending on:
- The client’s requirements.
- How many rooms are in the house.
- The presence of basements or additional stories.
Since more drywall sheets mean more drywall to tape and mud, you also need to calculate the materials you need to finish the job.
Since every drywall sheet needs around 1.5 to 2 pounds of mud, you may need up to 320 pounds of mud for a 2000-square-foot home. If the client requests more texture work, you’ll need even more mud.
How do you calculate sheetrock for a room?
You can calculate how many sheetrock or drywall sheets are needed for a room by dividing square footage by the measures of your sheet sizes.
For instance, a 10×15-foot room with a 9-foot ceiling height has a total area of 600 square feet. If you’re using 4×9′ (36 square feet) drywall sheets, you’d come up with the following equation:
600/36 = 16.67
Rounded up, you’d need 17 sheets. As a precaution, it’s a good idea to order extra sheets. Let’s say 19 to 20 4×9′ drywall sheets in total to cover an area measuring 600 square feet.
Fortunately, you don’t need to calculate all of this yourself. There are many web-based drywall layout calculators that you can use to estimate how many sheets you need to complete a job. However, you should always buy extra sheets just in case mistakes happen during work.
Get your free drywall estimate template here.
Image credit: stokkete via AdobeStock