Your guide to manufacturing process automation
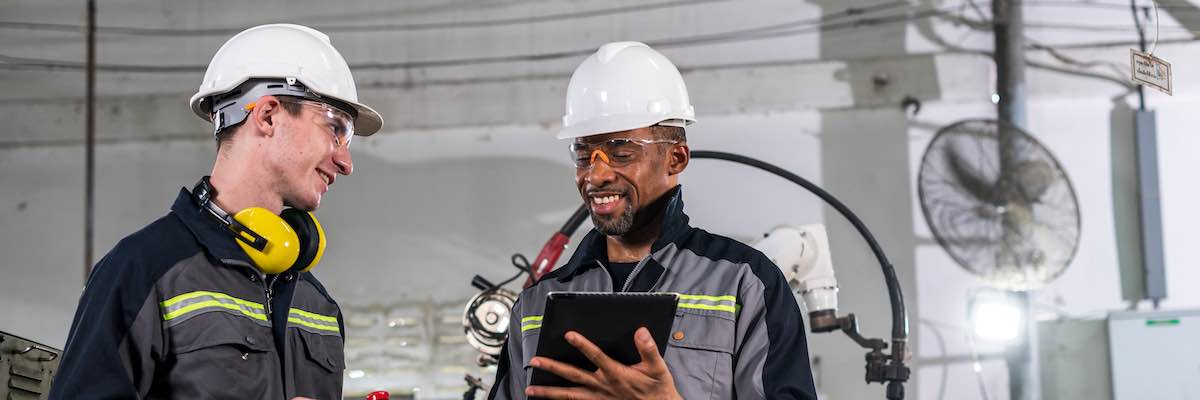
As the manufacturing industry continues to evolve rapidly, integrating automation is key to remaining competitive.
This guide covers everything you need to know about manufacturing process automation.
Dive in to learn about:
- The different types of manufacturing automation.
- When to automate your processes and not to.
- The many benefits of automation in manufacturing.
You’ll also learn about software to optimize your manufacturing processes and confidently embrace automation.
What is manufacturing automation?
Manufacturing automation is the process of integrating advanced technology into the manufacturing sector.
Drawing from our experience, by automating various production tasks, you can:
- Reduce manual labor.
- Increase efficiency.
- Boost precision and quality of your end product.
Picture this: cutting-edge robots and innovative machines work together, churning out products at lightning speed, while your employees focus on more creative and strategic tasks.
That’s manufacturing automation in action, and it’s revolutionizing businesses across the globe, from assembling cars to packaging food.
Types of automation in manufacturing
Now that you know what manufacturing automation is, let’s look at the types of technology transforming the industry.
Programmable automation
Programmable automation is fantastic for creating products in batches, ranging from a few dozen to several thousand units at a time.
Each new batch requires reprogramming and equipment changeover to accommodate the unique product style. Our team discovered that a production run for each new batch also follows a period of nonproductive time.
While this process takes time, its versatility makes it worthwhile.
But production rates in programmable automation tend to be lower in fixed automation since the focus is on product changeover instead of specialization.
Flexible automation
Flexible automation takes programmable automation to the next level by addressing its main disadvantages:
- Time-consuming reprogramming.
- Changeover for each new batch.
Based on our observations, with flexible automation, the product variety is limited enough for swift and automatic equipment changeovers.
Reprogramming happens offline, using a computer terminal separate from the production equipment.
This approach means there’s no need to group identical products into batches. Instead, you can manufacture various products right after another, making the process efficient.
Process automation
Process automation involves implementing advanced technologies to manage, control, and optimize various industrial processes.
With the help of sensors, programmable logic controllers (PLCs), and software, you reduce the need for human labor.
Manufacturing process automation also:
- Monitors production lines in real-time.
- Detects anomalies.
- Makes intelligent adjustments.
Process automation saves time and money and ensures that every product that rolls off your assembly line is high-quality.
Industrial robotics
Industrial robotics refers to durable and versatile machines that can perform numerous types of applications through programming.
Program parameters control robotic arms for productivity and precision.
Imagine programming your bots to repeatedly stack boxes onto pallets or transfer workpieces from one workstation to another. These intelligent robots can take on repetitive or hazardous duties so your workers aren’t at risk.
With tireless energy, this manufacturing process automation is effective when dealing with welding and robotic assembly.
Robotic process automation (RPA)
Robotic process automation (RPA) uses software to automate manual tasks, mimicking a human worker’s path.
It’s handy for rule-based processes like data entry or email management that consume valuable time.
Manufacturing businesses also often integrate RPA with technologies such as Artificial Intelligence and Machine Learning to make it smarter.
Machine learning and artificial intelligence (AI)
Machine learning refers to computer systems learning and improving from experience without further programming.
By analyzing vast amounts of data, these algorithms identify patterns and trends that are too complex for humans to detect.
This insight helps manufacturers:
- Optimize production processes.
- Reduce waste.
- Enhance overall efficiency.
Artificial intelligence is the broader concept of creating intelligent machines that perform tasks without human input. Manufacturing uses AI in many applications, such as robotics, computer vision, and natural language processing.
Combining AI with machine learning allows you to develop highly adaptive systems that make real-time decisions to optimize production processes.
Some examples of these futuristic technologies for manufacturing process automation include:
- Predictive maintenance — By analyzing historical data and real-time sensor information, AI-driven systems predict when a piece of equipment will likely fail, so you can anticipate maintenance and reduce downtime.
- Quality control — AI-powered computer vision systems inspect products rapidly, accurately identifying defects and inconsistencies to ensure consistently high product quality.
- Smart scheduling — Machine learning algorithms can analyze production data to optimize schedules, maximizing efficiency and reducing bottlenecks in the production line.
- Adaptive robotics — AI-enabled robots can learn and adapt to environmental changes, allowing them to perform tasks with greater precision and flexibility.
The difference between factory automation vs. process automation
The main difference between factory automation and process automation is that factory automation deals with individual components of the production line, such as robotic arms or conveyor belts. Process automation, however, analyzes the bigger picture to simplify workflows and maintain a smooth production environment.
Both contribute to a more cost-effective operation. While factory automation targets individual tasks and machines, process automation ties everything together, ensuring a seamless flow between different stages of production.
By harnessing the power of both types of automation, you can boost productivity, quality, and overall success.
When to automate a manufacturing process
Now that you know all about the different types of automation, you might wonder when to automate a manufacturing process.
Before you begin automating, you must first define your automation goals.
To ensure the benefits outweigh the costs, evaluate your operations and decide which areas lend themselves to automation.
Once you identify these areas, you’re ready to shape your manufacturing process automation strategy.
But before that, consider these three prerequisites:
- Setup and maintenance costs, including employee training on how best to use the automated system, and any associated hardware or software expenses.
- Sufficient human resources to monitor automated systems in case of issues or unexpected errors.
- A well-defined set of objectives to inform decisions during implementation and determine goal accomplishment.
When not to automate
You now know when to automate a manufacturing process, but sometimes automation isn’t the most suitable option.
For instance, human expertise is a better fit for complex production processes that demand specialized knowledge or intricate manual assembly.
Additionally, small-scale operations might not find automation cost-effective, as the high number of machines required or the absence of economies of scale make it an impractical choice.
In such cases, you can instead focus on enhancing efficiency by investing in employee skills development and training.
Automation may also not justify the return on investment for low-volume production operations.
If you don’t know your system inside and out, you risk wasting resources and having to make constant changes during development. Involving an automation architect early in the process helps prevent this.
The rise of manufacturing process automation
The manufacturing industry has experienced tremendous growth and technological advancements that made it possible to make products at scale.
Driven by innovation and a demand for greater efficiency, manufacturing process automation revolutionizes businesses’ operations. With the growing skills gap, modern factories continue to find new ways to implement automation.
Our findings show that manufacturing is one of the industries most impacted by automation. In fact, by 2030, up to 20 million manufacturing jobs around the world could be replaced by automation.
So what’s driving this change? Let’s look at some of the main advantages of automating manufacturing processes.
Benefits of manufacturing process automation
Focus on high-value work to accomplish more
With repetitive processes handled by automated systems, your workers can dedicate their time to improving efficiency or developing innovative designs.
One way to gain back time while setting up your business for growth through informed decision-making is to automate your reporting.
Revisit the webinar below to get caught up on best practices for reporting in the manufacturing and distribution industry.
Support your team with automation that connects your operations
Automation helps data flow seamlessly between departments, improving collaboration and informed decision-making.
A more cohesive and efficient work environment will also enhance your team’s performance and productivity.
Lower your costs
Aside from slashing the overhead costs of using human labor, automated machines generate much less heat waste than manual operations. How? They focus on controlled, precise movements with minimum power usage.
Overall, automating complex processes means you:
- Need fewer resources.
- Save time and money.
- Optimize your processes.
With manufacturing process automation software, you can cut costs and simplify your workflows even further.
Get started with the #1 manufacturing process automation tool for QuickBooks and Xero users
Method is your best option for manufacturing process automation for QuickBooks and Xero users. Its powerful, two-way sync streamlines your manufacturing processes and ensures accurate and up-to-date data.
WIth Method, you get::
- Real-time inventory management to effortlessly track raw materials, finished products, and work-in-progress.
- Simplified order management to reduce manual work and minimizes errors.
- Enhanced customer service and personalized support to strengthen your client relationships.
In the video below, check out how an integration with Method helped double this shipping container company’s revenue in just three years.
Recap: The value of manufacturing process automation
In today’s rapidly evolving manufacturing industry, manufacturing process automation helps you compete.
Some of the many benefits of automation in manufacturing include:
- Slashing your costs while boosting efficiency.
- Improving collaboration through seamless data flow.
- Higher volume and enhanced product quality.
Automation software like Method can streamline your manufacturing processes so that you can confidently grow your business.
Save hard costs and real time with your free trial of Method.
Image credit: Lukyeee_Nuttawut via Adobe Stock